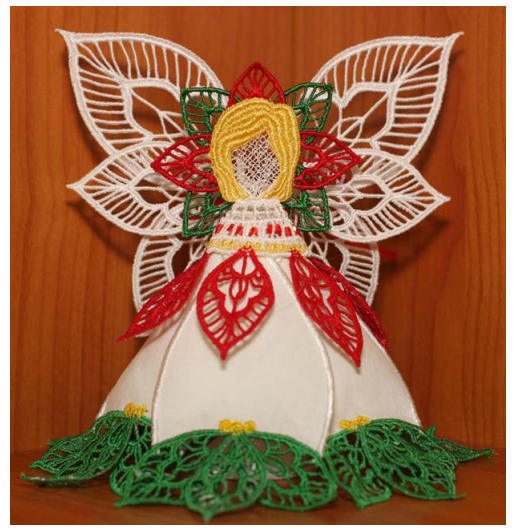
This exquisite Poinsettia Angel features free-standing machine embroidered lace combined with appliqué panels on her skirt. The wings can be embroidered as either free-standing lace (as shown) or embroidered onto Twinkle Organza for a shimmery, gossamer effect. This angel can beautifully top off your Christmas tree or become the magnificent focal point on your mantle or holiday table. Make her as special gift for someone special—which just might be you!
Appliqué is personally one of my favorite techniques. It is relatively easy and can add texture, pattern, and colors that aren’t available in thread. And it can significantly reduce stitch counts. Here I’ve used appliqué on the skirt, part of which is hidden under the lace yoke. Having a solid area there allows the intricate lace detail to be more visible.
This project assumes you have some experience with embroidering lace. I have a included beginner tutorial with Winter Jewels Mock Crochet Snowflakes, which are geared for beginner embroiderers.
These instructions focus on assembling the angel and include only basic instructions on the featured techniques.
Featured Techniques
- Free-Standing Lace
- Free-Standing Appliqué
- 3-D Appliqué with Free-Standing Lace
Instructions
This design project includes multiple pieces and techniques. Please read through the directions first. Also, plan time to make this angel. Although not technically difficult, she does require attention to detail and time. You’ll need sewing time, drying time, and assembly time so do allow more than a quick afternoon make-it, take-it kind of project.
Please read all instructions before beginning!
Abbreviations
- TESA Temporary Embroidery Spray Adhesive
- FSL Free-standing Lace
- FSA Free-Standing Appliqué
- 3DA 3D Applique
Supplies
For embroidery:
- Poinsettia Lace Angel designs
- Small amount of fabric (fat quarter) for skirt appliqués (must be compatible with water to allow stabilizer removal)
- Embroidery machine with minimum 130 x 180mm (5x7”) sewing field
- Embroidery thread: These designs were digitized and tested with 40 weight embroidery threads (SoftLight Metallic, Rayon, polyester, cotton)
- Bobbin thread: I used regular embroidery bobbin thread (for best results, wind on the bobbin your machine prefers if prewounds aren’t providing optimal results).
- Needles: embroidery needle to accommodate thread. I used a 75/11 Schmetz. I do not use a metallic needle with metallic threads.
- Water soluble non-woven fiber based stabilizer (Hemingworth Wash-Away and Sulky FabriSolvy are my two favorites)
- Optional (but very useful!): thread stands
- TESA (I prefer KK2000)
- Cellophane tape
For drying:
- Wire cookie drying rack
For Finishing:
- Fine-tipped hot glue gun
- 2 strips quarter inch wide ribbon (24” eachis sufficient); can be same or different colors
- Tapestry needle for lacing ribbons
- Clamp-type paper clip or clothes pin
Optional and Useful
- Light table
For Embellishing:
- Optional: glitter glue, white glue and glitter, tiny hot-fix crystals, bead, ribbon or decorative cord for hanging
Abbreviations
- TESA - Temporary Embroidery Spray Adhesive
- FSL - Free-Standing Lace
- FSA - Free-Standing Appliqué
- 3DA - 3D Appliqué
- SPM - Stitches per minute
The Designs
This collection includes 10 design files, which are numbered in the approximate sewing order:
- lgp00301 - Single leaf (useful if you have to replace one or want to test your technique first)
- lgp00302 - 7 individual leaves combined (fits 5x7 hoop)
- lgp00303 - single skirt panel, for 5x7 hoops
- lgp00304 - 3 skirt panels combined for larger hoops
- lgp00305 - dress yoke
- lgp00306 - head
- lgp00307 - 3-point halo
- lgp00308 - 4-point halo
- lgp00309 - large back wing segment (mirror for opposite side)
- lgp00310 - middle forward wing section
Some formats will be missing some files because they are too large for your sewing field. This is why the DST format is always preselected and you should download it with your desired formats.
Preliminaries
Detailed instructions are not included for the various techniques. If you need more instructions please check the website or YouTube for free help:
General Instructions Overview
For those of you who don’t like to read directions, please at least read these general instructions to save yourself a little frustration. Those of you who need more guided assembly instructions can keep reading.
Some designs need to be sewn in a specific order. For example, the pieces used as 3D appliqués need to be sewn before the piece to which they are attached. Make sure you understand the sewing order, too, if you decide to combine pieces into one hoop.
- The leaves are attached to the skirt panels; sew leaves in a separate hoop before the skirt panels.
- The 3-point halo is a 3D applique attached to the 4-point halo; sew the 3-point halo in a separate hoop before the 4-point halo.
The sample shows 6 skirt panels, which are attached to the yoke by lacing with a ribbon. The double layer halo section is hot glued to the back of the head, which simply sits inside the skirt neck opening. The large wing segments are hot glued to the back of the small center wing segment. The yoke extensions meet in the back to form a back dress placket and are laced to the wings with ribbon.
All pieces of this project are sewn on two layers of water-soluble stabilizer. Feel free to use colors of your choice; the Poinsettia Angel would look elegant sewn monochromatically in ivory.
I prefer to match the appliqué thread to the fabric color but please yourself. You can totally change the character of your angel by altering the colors, threads, and fabrics you choose.
Step 1: Sewing
1. Make the Skirt Panels
The sample shown uses 6 skirt panels. You may choose to sew more or fewer. Each skirt panel is a 2 part appliqué.
1. The main fabric skirt section is appliquéd directly to the stabilizer.
2. The second appliqué is the center lace leaf motif, which is attached with the berry elements.
Therefore, you need to embroider the leaves before embroidering the skirt panel.
Center Leaves
There are two leaf design files. The first one is just a single leaf motif. This single design is included for test your machine for optimal tensions, if your machine is not getting results with the combined group, and if you just need to replace a leaf that didn’t sew out well.
The second combines 7 leaves which will fit a 130x180mm hoop or a round hoop on multi-needle machines. DO NOT COLOR SORT THIS FILE. Yes there are only two colors and yes, they repeat for each leaf. This method results in better registration, a critical factor in successful lace designs.
There are 7 leaves because this fits the 180 round hoop on my machine perfectly and also filled the 130 x 180 hoop nicely. It gives you one extra leaf so you can choose the 6 best ones or, if the first 6 sew out perfectly, stop before sewing the last one.
Sew the leaves as standard FSL. Cut out the leaves close to the stitching and do not remove the stabilizer
Skirt Panels
These appliqués were designed to work best with precut appliqué pieces using the included template. This is my favorite method for appliqué because it gives a clean, crisp, professional result with no little pokie fibers jutting out from the satin edges.
1. Print out the PDF template at actual size (Page Scaling: None) from Acrobat.
2. Apply the template to the FRONT side of prepared fabric (preshrunk, pressed, starched).
I prefer to print on fusible tear-away in an ink jet printer then iron the pieces to the fabric. This reduces the chances of slipping. You must cut your fabric EXACTLY like the template! If your fabric cannot tolerate heat, use TESA to secure the template to the fabric.
3. Cut out appliqué pattern EXACTLY along the outside edge of the outline.
4. At the machine, sew the placement guide (color 1). The machine should then stop, usually at the top of the appliqué area (left or right side of hoop on combined skirt panels file).
5. Remove the paper pattern from the appliqué, mist the back of the fabric lightly with TESA
and precisely align the pre-cut appliqué piece over the stitched outline making sure it won’t shift during the tack down process. Continue sewing.
6. ACCURACY THROUGHOUT THESE STEPS IS CRITICAL!
You may want to slow the machine down during the tack down in case you need to make some placement adjustments. Stop the design after the tack down sews and trim off any fabric that extends beyond the tack down. Attention to detail here will give you clean professional-looking appliqués with no “pokies” extending beyond the stitching.
Continue sewing the skirt panel up to the second appliqué stop. The last color sewn at this point will be the outlines for the berries, which are just placement guides. Align the berries on the cut out leaf motif over these guides and tape the leaf in place with regular cellophane tape outside of the sewing area (berries).
Sew the final color. Your skirt panel is complete. One down, five to go!
2. Make the Halo
The halo is a two piece 3D applique similar to the skirt bottom. Sew the 3-point halo first and cut out around the outer edges only.
Sew the 4-point halo up to the appliqué stop. Take the hoop out of the machine; do not unhoop the fabric. Line up the 3-point halo over the 4-point so that the center petal/bract is aligned vertically and the center circles exactly match.
This is where a light table comes in handy. Tape each top petal to hold the top piece in place. Return the hoop to the machine and sew the last color, which is a satin stitch over the circle attaching the two pieces together.
3. Sew Remaining Pieces
All the other pieces are sewn flat, with no special techniques. Be sure to mirror the large wing and sew again for the other side.
Step 2: Removing Stabilizer
Before removing stabilizer, clean up any thread tails and allow any TESA to fully dissipate. You can speed this process with a warm dry iron but do keep in mind heat will shrink the stabilizer. Don’t panic though, because you are going to wash it out in the next step. Just make sure you don’t press in any permanent creases into the fabric.
Refer to your product’s instructions for water temperature and any special requirements. Avoid over-soaking, especially on the full lace pieces. Simply rinse until you don’t see any stabilizer remaining, the extra remaining stabilizer will add support to your angel. It will probably feel gooey when you take it out of the water.
t is vital that the yoke and center wing extensions remain as stiff as possible since this supports the wing structure.
After rinsing, smooth out pieces on an absorbent, lint-free towel and roll or blot to remove excess moisture; do not wring lace. Lace pieces can then be laid on a wire cookie cooling rack to dry or be shaped or blocked over non-stick items as desired. (I dried mostly flat, curling the petal tips slightly). You will probably need to press the skirt panels to smooth them out when dry.
I used red silk for one angel’s skirt. Because this fabric bled when placed in water, I chose thread colors that would not be affected by any bleeding. And if you’re wondering about water spots on the silk… I soaked the entire piece in hot water before appliquéing so I guess that made it one giant water spot!
Embellishments
Once fully dry, feel free to embellishing with hot-fix crystals, sequins, glitter, etc. This is easier to do before assembling your angel.
Assembling the Poinsettia Angel
Skirt & Yoke
The skirt panels are attached to the yoke by weaving with ribbon through the Richelieu bars on the yoke section. There’s no real science to this; I chose to center the skirt panels under the petals on the yoke. Leave enough length on each end to tie a bow. The piece I used was about 24” long.
Pay attention that you attach the skirt panels right side up!
Some Helpful Tips
1. Start in the middle of the yoke with the center front skirt panel. Pull up half the length of the ribbon and secure on end with a paper clip.
2. Weave in all the panels to one side of the center, then do the other side.
3. The skirt panels are woven to the under side of the yoke. When weaving, weave over the outer bars for a more secure and stable connection.
4. The last panel gets woven on to the last few segments on one side; it doesn’t matter which.
Halo & Wings
The halo is centered behind the head with the lower part of the circle matching her chin. Hot glue in place in the hair area. Form the petals as desired.
The large wing segments are hot-glued to under the center wing segment. Match the area between the upper and lower wing to the center wing’s cross piece. Angle the segments as you wish.
Final Assembly Steps
Wrap the skirt sections around so that the horizontal yoke extensions align with each other to form the back placket of the dress. Match the wing extension over the placket and lace up with the second piece of ribbon. (I used white in this sample.) Before tightening the laces and tying the bow, insert the head into the neck opening.
I laced the white through the same slots as the red, then up one more (white only on top). I also alternated the cross-overs of the shoe-lace “x” with the white. How you lace is not as important as just securing her together. This section acts like the spinal column for the angel.
Once assembled, arrange and shape her wings as desired. Fan out her skirt panels. If the skirt doesn’t have enough body to support her upper section, you might want to use more stiffener in the skirt or just create a small cardboard “petticoat” to support her.
I left her skirt panels free-floating. If this bothers you, you can attach them as you choose—maybe tacking them with a small embellishment like a button or a small ribbon bow, or a bead or two.
Other Tips
I don’t recommend combining lots of multiple pieces in the hoop, especially with the larger or higher stitch count elements. If you do choose to do this, secure the stabilizer well (duct tape is very useful), and don’t color sort. Sew each design through entirely before moving to the next repeat.
Design Notes
Although I’ve digitized this as multi-color, you can easily sew the elements monochromatically or mix up the colors to suit your own tastes. On poinsettias, although we often consider the red part to be the flower, these are actually modified leaves. Don’t feel restricted to keeping the “leaves” on the skirt green and the “leaves” on the yoke red. Poinsettias come in a range of shades from creamy white through solid and mottled pinks and reds, even blue and black!
I simply used standard white embroidery weight bobbin thread, you may choose to wind bobbins to match the top thread. Keep in mind unless you find a very fine matching color, the matching bobbin thread is likely to be heavier and therefore add bulk to the embroidery.
You can also change the look of your angel by fabric selection in the appliqué areas. If your fabric choice is too thin or ravels easily consider using a fusible web to fuse multiple layers together. You could even choose a piece of lace for the skirt and underline it with organza.
You can also choose to embroider her outer wings on organza and then cut out. Nylon Twinkle organza comes in a wide range of colors.
Trouble Shooting
These designs have been thoroughly tested on multiple machines using the techniques included here. All testing was done with 2 layers of stabilizer; one layer simply does not stand up to machine tensions enough for free standing lace designs. (If you are sewing on another stable fabric, one layer is generally sufficient.)
If your lace is falling apart in some areas and you did not resize or otherwise alter the design and you followed the above instructions, it is generally an indication of:
- Overly tight machine tensions (the higher the SPM, the tighter the tensions; slow your machine down!). This is especially true if designs are consistently falling apart in multiple areas.
- Overly loose stitches are another tension problem and are more apparent on enlarged designs and when using finer thread.
- Poor hooping technique. Stabilizer should be firmly and evenly gripped all around the hoop and must not be ripply, saggy, or puckered.
- Stabilizer slipping during sewing. This is more likely with thin, slippery stabilizers (like Aqua Cloth), with distorted hoops, and larger hoops. Use some method to prevent slippage. Stabilizer slippage is further exacerbated with tight machine tensions and high SPM.
- Skipped stitches at an inopportune time (possibly a needle problem). If this happens frequently or it has been a while since you changed the needle, change it now!
- Thread catching or not feeding evenly. If a thread loop catches on your machine or the spool cap is not smooth and snags the thread, enough tension can be generated to cause a stitch to be shorter than it would under normal circumstances. Use a thread stand, thread net, or other method for insuring a smooth thread delivery to the needle.
If you cannot control your machine finely enough, it may be necessary to edit the design for that particular machine. Please note that if you do this, only work on a copy and only adjust as needed. Stitches that are overly compensated will look sloppy and detract from the beauty of your design.
Similar Designs
The Poinsettia Angel is the second angel of the heirloom lace angels. If you’d like the first one that is all lace, check out the Heirloom Lace Angel displayed on the top of my tree. You might enjoy this show-stopping, free-standing lace angel. At approximately 8.5” tall, she requires a minimum 130mm x 180 mm sewing field (5x7 hoop) for embroidering, preferably a 200mm x 300mm hoop for easiest method. You’ll get all the designs plus full instructions in this project collection. Download here.
The snowflakes are a set of 15 “mock crochet” FSL designs and stitch up quite quickly with much lower stitch counts than comparably sized lace ornaments. This collection also includes full instructions along with a tutorial on lace—perfect for newer embroiderers.